C’est bien beau d’avoir une poignée de T-Beams et T-Lora pour jouer avec Meshtastic, mais il faut les loger !
Un fois les tests de portée effectués, il fallait des boitiers un peu ergonomiques pour pouvoir balader les montages dans un sac de randonnée par exemple. Comme je voulais quelque-chose de compact je suis parti sur un boitier qui contiendrait à la fois la carte Lilygo et l’antenne pour que rien ne dépasse.
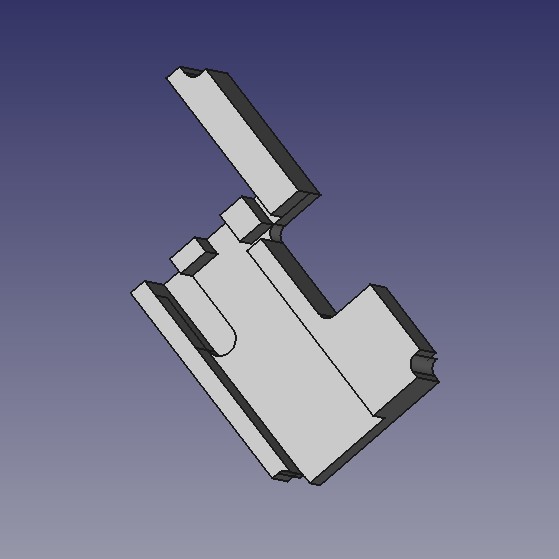
Modélisation avec FreeCAD
Pendant la construction de mon rover RTK je me suis demandé comment caler les composants dans le boitier plastique sans que ça bouge trop et j’ai eu l’idée d’utiliser des plaques de polystyrène qui devaient servir d’isolation thermique dans des caisses de médicament si je ne dis pas de bétises. Ces trucs se façonnent assez bien au cutter mais quand on dispose d’une petite graveuse d’entrée de gamme, pourquoi ne pas l’utiliser pour ça ?
Tout commence par la prise des cotes au pied à coulisse, et à la modélisation du volume final de polystyrène dans FreeCAD. J’avais fait quelques trucs avec FreeCAD mais sans jamais aller bien loin, ça ma donné l’occasion de m’y remettre sérieusement, merci aux vidéos tutorielles trouvés sur Internet.
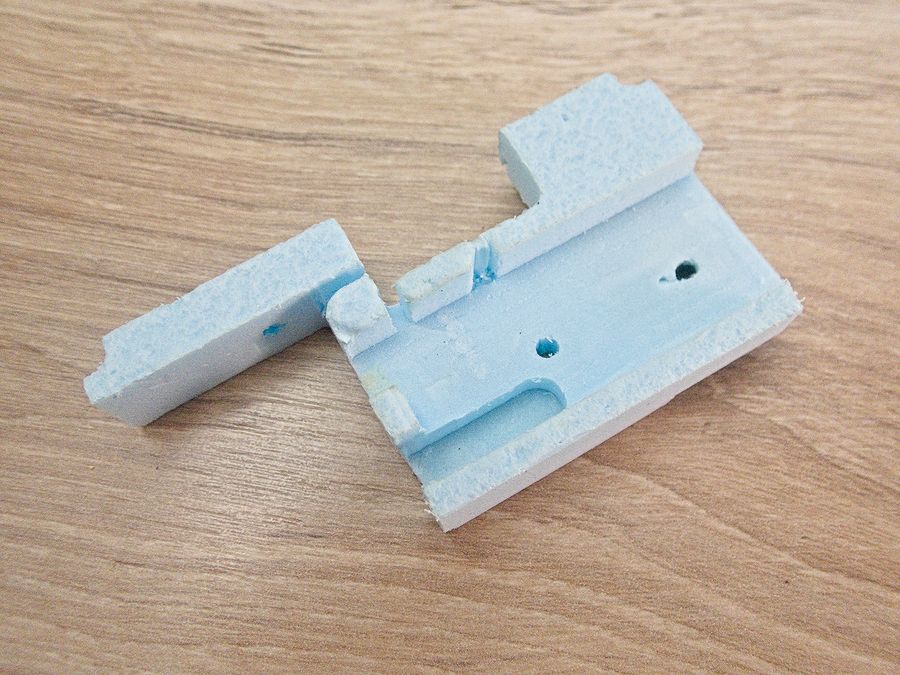
Vue de dessus de la pièce usinée (j’ai dû faire un peu de tuning au cutter parce que j’avais oublié des trucs -__-)
Je crée des fichiers pour les deux fraises que je vais utiliser (1 mm et 3 mm) et après un peu de pataugeage je peux sortir le G-Code correspondant aux surfaces que je veux usiner ou surfacer.
Après avoir joué avec la vitesse d’avance je sors péniblement la pièce finale en mousse (attention aux très fines poussières de polystyrène, ça n’a pas l’air très bon à la santé).
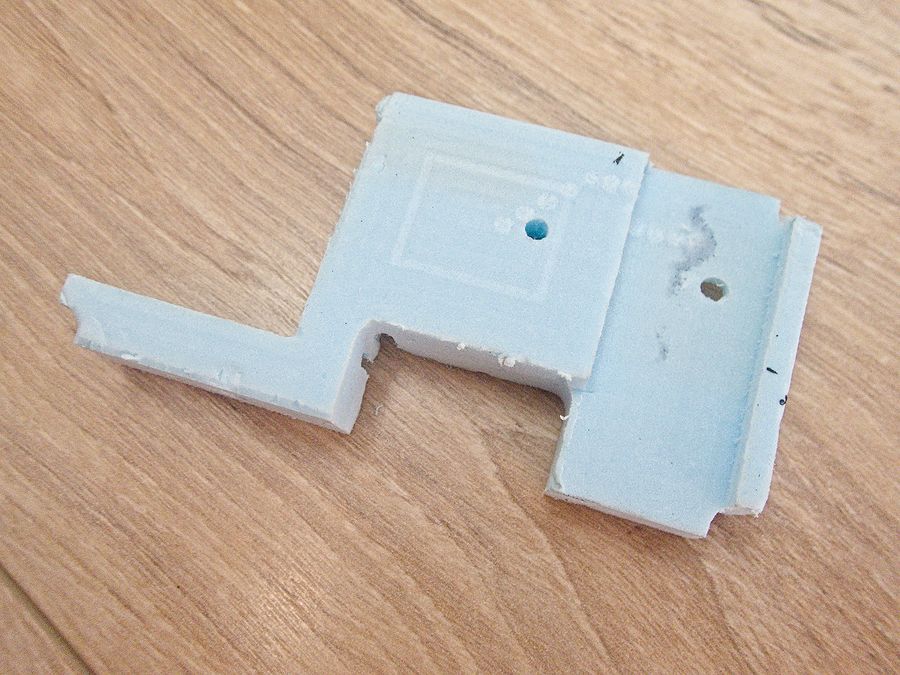
Vue de dessous de la pièce usinée (après deux ou trois montages-démontages elle est un peu abîmée)
Enjoué par ce succès je prends la confiance et je m’attaque aux perçages dans le boitier ABS. la 3018 a un débattement un peu juste sur le Z donc je triche pour serrer la fraise de 1 mm dans le mandrin. Le boitier n’est pas vraiment un parallépipède mais plutôt un lingot alors il faut faire un petit calcul et caler la MAP avec des cartons pour corriger l’assiette mais ça passe.
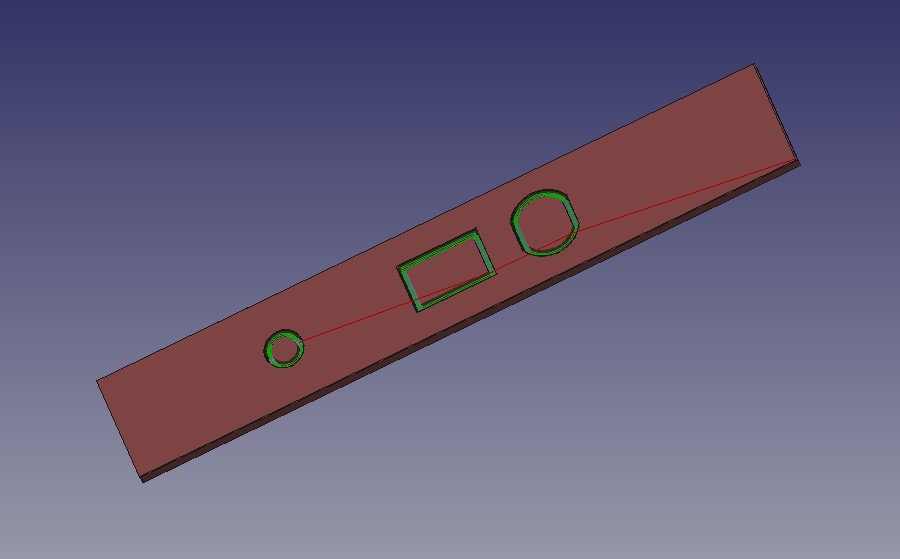
Les usinages de la tranche du boitier
Des grosses vibrations pendant l’usinage, mais je suis content du résultat, les méplats pour la prise USB-C sont très efficaces. Et oui je n’ai pas encore mis la LED (en fait je ne sais pas comment la brancher).
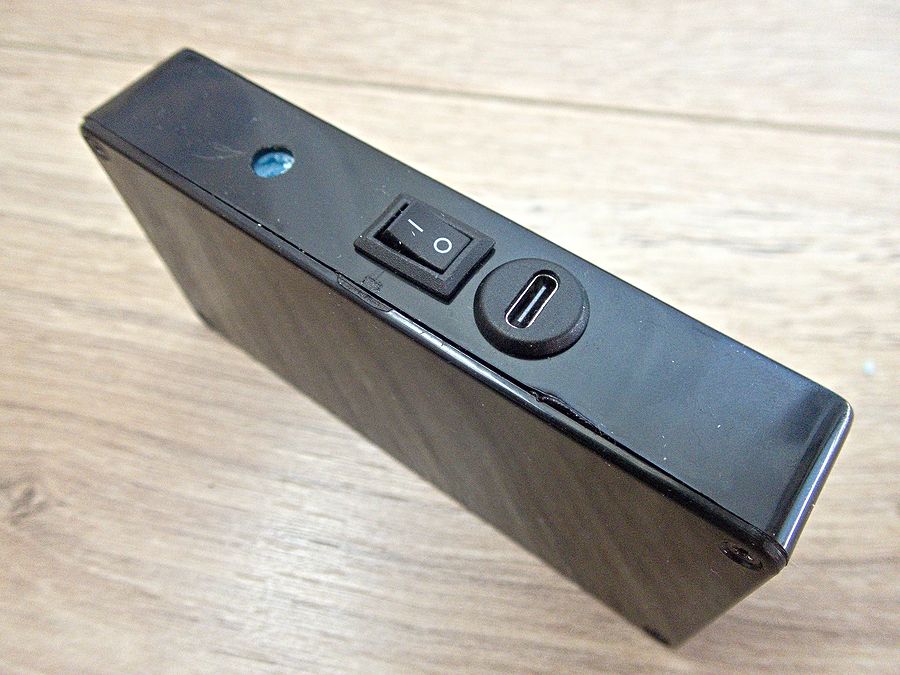
Le boitier monté (ou j’ai fondu accidentellement le plastique avec mon fer à souder -__-)
Conclusion ? Beaucoup de travail pour un résultat que j’aurais probablement pu faire en quelques coups de cutter et à la mini-perçeuse, mais je suis content du rendu !